Ultimate Guide on 3D Printing with ABS Filaments and its Variations [2024]
- Diana Velyka
- May 14, 2024
- 18 min read
Updated: Oct 25, 2024
ABS Filament is one of the most used 3D materials these days. Famous for its strength, gloss, and toughness, this 3D printing filament is suitable for a variety of technical applications. Therefore, we have collected all the useful information about this 3D printing plastic material in this post.
Whether you're just starting your 3D printing journey or looking to expand your material knowledge, this blog post will guide you through everything you need to know about ABS filament.
We've got you covered! Learn ABS 3D printing applications, its benefits and disadvantages, get tips on improving the printing process, and find out what filament alternatives you can use.
Keep reading to discover ABS filament and its best usage for you!
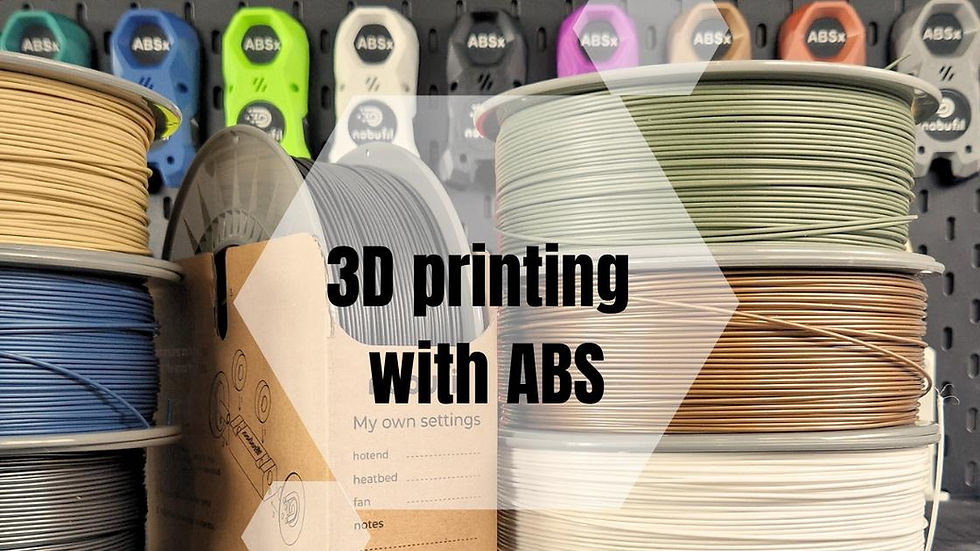
What is ABS Filament?
ABS, or Acrylonitrile Butadiene Styrene, is a thermoplastic polymer widely used in 3D printing. It's known for its high strength, gloss, and toughness, making it a preferred choice for a wide range of applications. ABS melts at a higher temperature than PLA 3D material, enabling it to withstand higher temperatures without deforming. This characteristic, coupled with its slight flexibility, allows for the creation of durable and resistant 3D printed items.
Despite its many advantages, ABS can be slightly more challenging to work with than some other 3d filaments. It requires a heated bed and ideally an enclosed printer (unless it's Nobufil ABSx) to prevent warping and ensure proper adhesion during the printing process. However, with the right printing settings and a little practice, ABS 3D filament can produce exceptionally strong and durable prints.
Advantages and Disadvantages of 3D Printing with ABS
Despite plenty of applications that this 3D material offers, ABS filaments have their advantages and disadvantages at which you need to pay attention in choosing the right 3D printing material. Here’s a deeper dive into what makes ABS a popular choice for many, as well as what challenges it might pose.
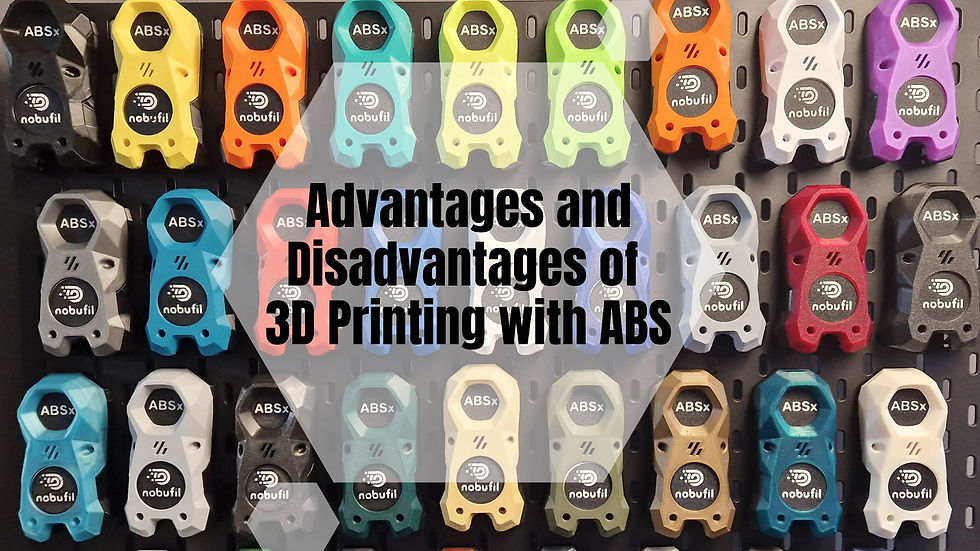
Advantages of 3D Printing with ABS
Here are advantages of ABS Filaments:
Durability and Impact Resistance: One of the standout features of ABS 3D material is its strength and ability to withstand significant wear and tear. This makes ABS an excellent choice for creating durable parts and functional prototypes that must endure stressful conditions, outperforming many other materials in terms of toughness.
High Heat Resistance: With a higher melting point than many other plastics used in 3D printing, ABS is less likely to deform when exposed to hot temperatures. This characteristic is especially valuable in applications such as automotive parts, electronics housings, and kitchen gadgets, where heat resistance is critical for safety and longevity.
Finish Options: The aesthetic versatility of ABS material is also noteworthy. It can be easily sanded, painted, or smoothed with acetone vapor, allowing makers to achieve professional-level finishes on their prints. This capacity for post-processing opens up a world of possibilities for customizing the appearance of ABS prints, whether for artistic projects, consumer products, or functional prototypes that need to look as good as they perform.
Chemical Resistance: ABS 3D material exhibits good resistance to many chemicals, including certain acids and bases, making it suitable for applications in environments where exposure to chemicals is a possibility. This chemical resistance is superior to materials like PLA, which may degrade more rapidly when exposed to certain substances.
Electrical Insulation Properties: ABS is an excellent insulator against electricity, making it a preferred choice for electronic housings and components where electrical insulation is required. This property distinguishes ABS from conductive or semi-conductive materials, offering unique advantages in electronic applications.
Disadvantages of 3D Printing with ABS
Now when we spoke about pros of 3D printing with ABS Filaments, let’s have a look at its cons.
Printing Difficulty and Equipment Requirements: ABS printing process can be challenging due to its need for a heated print bed and a controlled printing environment to prevent warping and ensure proper adhesion. It means that you will need to have specialized equipment, like a 3D printer enclosure (if your 3D printer does not include it) to maintain consistent temperature.
Unless you use Nobufil ABSx 3D material, which is a modified and more sustainable ABS and can be also 3D printed on a printer without enclosure.
Emission of Fumes: During the printing process, ABS emits strong fumes that can be unpleasant and potentially harmful without proper ventilation. This necessitates a well-ventilated workspace or specialized filtration systems, making it less desirable for use in poorly ventilated areas or educational settings.
Sensitivity to UV Light: ABS parts are sensitive to prolonged exposure to UV light, which can lead to degradation and color change over time. This limits its use in outdoor applications or in environments where the material would be exposed to sunlight for extended periods, unlike UV-resistant materials like ASA that are specifically designed for outdoor use.
Warping and Dimensional Accuracy: ABS filament is prone to warping, which can affect the dimensional accuracy of the final print. This characteristic can be particularly challenging when printing large or flat parts, requiring additional measures like brims or rafts to mitigate the issue. Materials like PETG, on the other hand, offer similar strength with less propensity for warping, providing an alternative for applications where dimensional stability is critical.
Ideal 3D printing Applications for ABS Filament
ABS material in 3D printing is incredibly versatile, making it suitable for a variety of applications, particularly where durability and temperature resistance are key.
It the material of choice for functional parts that demand robustness and reliability, such as:
Gears: Ideal for mechanical systems requiring high durability.
Enclosures: Protective casings for electronics and machinery.
Automotive Components: Including car interiors, dashboards, consoles, air vents, and custom modifications.
Electrical Housings and Covers: Providing protection for electrical circuits and components.
Tool Handles and Holders: Offering strength and resistance for workshop tools.
Electronic Device Cases: Such as casings for phones, radios, or computers, where toughness is essential.
3D Printer Parts: Like the Voron printer parts, Bambulab AMS, and printer casings, benefiting from ABS’s heat resistance.
Vehicle Bumpers: Capable of absorbing impacts due to its high toughness.
Plumbing Components: Including pipes and fittings, where ABS's water resistance is advantageous.
Functional Prototypes: Allowing engineers and designers to test concepts in real-world conditions.
Terminal Blocks: ABS is the material of choice for these popular toys, known for their precise fit and durability.
Sporting Goods: Such as helmets, guards, and equipment parts, requiring impact resistance.
Musical Instruments: For parts that need to be durable and able to withstand handling and environmental stress.
Custom Containers and Boxes: Tailored storage solutions that are durable and can be designed to fit specific needs.
Robotics Components: For durable and reliable parts in robotics projects or educational kits.
Education and Art: Artists and designers use ABS filaments to create sculptures, art installations and unique works of art with post-processing.
Kitchen Gadgets: Items that need to withstand heat and frequent use.
Medical and Healthcare: custom prosthetics, orthotics and medical device prototypes.
Custom Fittings and Brackets: For construction or DIY projects where standard sizes do not suffice.
Safety Equipment Parts: Including components for protective gear and devices.
Aerospace: prototyping and manufacturing lightweight components, cabin interiors, and UAV (Unmanned Aerial Vehicle) components.
The array of possible applications for ABS filament underscores its importance in both industrial and hobbyist 3D printing, offering the perfect blend of performance and versatility. Whether it's for creating durable everyday items or for specialized projects requiring a robust material, ABS filament stands out as a top choice.
Nobufil ABSx Filaments feature enhanced precision, allowing for intricate details, making them ideal for hobbyist projects that require fine detailing. For example, for 3D models with a lot of small details you want to highlight.
In the world of custom fabrication and DIY projects, ABS 3D printer filament ability to be easily sanded, drilled, and painted makes it a highly adaptable material. From personalized gadgets and tools to bespoke fittings and fixtures, ABS can be transformed to meet the specific needs of virtually any project.
3D printing ABS filament: What are the best settings for ABS?
When 3D printing with ABS material, getting the right settings is crucial for success. The settings usually vary, based on the ABS filament brand and printer you have.
However, pay attention to these key parameters:
Print Temperature: Good ABS Filament typically requires a higher extruder temperature than other 3D filaments. Usually the printing temperature is between 240°C and 260°C. The exact temperature may vary depending on the printer and filament brand, so it is recommended starting at the lower end and adjusting based on the print quality.
Bed Temperature: A heated bed is essential to prevent warping. The bed temperature for ABS 3D printing should be set between 90°C and 110°C to ensure good first-layer adhesion and reduce the chances of warping as the print cools.
Print Speed: A moderate print speed of around 40-60 mm/s is ideal for ABS printing. Slower speeds can improve adhesion and print quality, while faster speeds may lead to issues like poor layer bonding and inaccuracies.
Cooling Fans: Unlike PLA, ABS prints better with minimal cooling to prevent warping and ensure good layer adhesion. If your printer has cooling fans, consider turning them off or significantly lowering their speed.
Enclosure: Using an enclosure to maintain a consistent and warm environment around the print can greatly improve print quality by minimizing warping and temperature fluctuations.
The best ways to print ABS material: Tips to improve your prints
To make better the quality of your 3D prints with ABS printer filament, and to make the printing process smoother, consider these tips:
Use an Enclosure: Enclosures help maintain a stable temperature, reducing warping and splitting. If you don't have a commercial enclosure, a DIY solution can also work effectively.
Apply Adhesion Helpers: Use adhesives on the print bed, such as ABS juice (a mixture of ABS scraps dissolved in acetone) or a commercial 3D printing adhesive, to improve first-layer adhesion.
Level the Bed Precisely: A well-leveled bed is crucial for successful first-layer adhesion. Take the time to level your bed accurately, especially before a large print.
Opt for a Raft or Brim: Adding a raft or brim can significantly improve adhesion to the print bed and minimize warping, especially for large prints or those with small footprints.
Monitor the Temperature: Keeping a consistent temperature inside the printer or enclosure is key. Avoid drafts or sudden temperature changes by placing the printer in a stable environment.
Troubleshooting for ABS 3D Printing Problems
Even with optimal 3D printer settings, you can still experience issues when printing with ABS filament. Here's how to troubleshoot common ABS printing problems:
Warping: If the corners of your print are lifting, consider increasing the bed temperature, using an enclosure, or applying additional adhesives to the print bed. Ensure the printing environment is free of drafts.
First Layer Not Sticking: First layer adhesion is critical for a successful print. If the first layer isn't sticking well, besides using adhesives or a raft, ensure that the nozzle is close enough to the print bed during the first layer. A slight decrease in the nozzle-to-bed distance can improve adhesion without causing the nozzle to scrape against the bed.
Poor Layer Adhesion: Increase the extruder temperature slightly to ensure the ABS is fully melted and adheres well between layers. Reducing the cooling fan speed or turning it off can also help.
Cracking or Splitting: This typically occurs in taller prints due to temperature differences between layers. An enclosure can help maintain a consistent temperature around the print. Also, consider increasing the extruder temperature slightly to improve layer bonding.
Stringing or Oozing: If you notice stringy prints or excess material oozing from the nozzle, try reducing the extruder temperature by 5-10°C increments, or increase retraction settings to pull filament back during travel moves.
Nozzle Clogs: ABS material can occasionally lead to nozzle clogs, especially if the filament contains impurities or if you're printing at too low a temperature. To prevent this, ensure your filament is high quality and your nozzle is heated to the correct temperature for ABS. If clogs occur, try a cold pull method or carefully use a needle to clear the nozzle.
Surface Quality Issues: For issues like rough surfaces or lack of detail, check your printer's calibration, particularly the extrusion multiplier or flow rate settings. A fine-tuned calibration ensures that the right amount of filament is extruded. Additionally, for a smoother finish on ABS prints, consider acetone vapor smoothing as a post-processing method, but remember to use it in a well-ventilated area and follow safety precautions.
Brittle Prints: If prints are coming out brittle or weak, it might be due to moisture absorption in the filament. ABS can absorb moisture from the air, affecting its printing properties. Store your ABS filament in a dry, airtight container with desiccants to keep it dry. If moisture has been absorbed, drying the filament in a filament dryer or an oven at a low temperature for several hours can help restore its quality.
Blobs and pimples: To tackle those pesky blobs and pimples when printing with ABS, it really boils down to tweaking a few settings and keeping your printer in tip-top shape. Start by playing around with the retraction settings — this helps stop any unwanted dribbles of filament. Then, see if you can lower the printing temperature a bit; it's all about finding that sweet spot where the filament behaves. Slowing down your print speed can also give your piece a chance to cool off properly, avoiding those little blemishes. Features like coasting and wiping are your friends here, gently nudging the filament to stop exactly where you want it and keeping the nozzle clean for a flawless print. Don't forget about using Z-hop to lift the nozzle away from the print, avoiding any accidental nudges. And, of course, a clean printer is a happy printer, so keep that nozzle clear to ensure smooth printing. A few adjustments here and there, and you'll be well on your way to smoother, cleaner prints.
Remember, the key to successful ABS printing lies in experimentation and fine-tuning settings based on the behavior of your specific printer and filament. Taking the time to test and adjust can lead to consistently better prints with ABS Filaments.
ABS 3D Filament vs ABSx Filaments
Probably you have already seen in different 3D printing communities the mentions of ABSx material. Let’s have a look at this new innovative 3D material created by Nobufil.
ABSx filaments (those are Nobufil ABS), are engineered versions of ABS 3D material that aim to enhance certain aspects like better layer adhesion, reduced warping, lower odor emissions and higher print detailing. The "x" in ABSx stands for various enhancements made to the base ABS polymer to meet specific needs or overcome common printing challenges associated with standard ABS material.
The special material formula also makes the 3d printing process with this ABS filament much easier. For example, ABSx Filament doesn’t require an enclosure for nicer prints. It prints super easy conserving high toughness, durability and heat resistance of the parts.
Both ABS and ABSx filaments are suitable for printing durable, functional parts. However, with its improved printability and potentially enhanced properties, ABSx can be more accommodating for users who are new to 3D printing or those without access to high-end printing setups. It broadens the range of projects where ABS's advantages can be utilized without its usual drawbacks.
One of the significant drawbacks of printing with ABS is the strong, unpleasant odor it emits, attributed to the volatile organic compounds (VOCs) released when heated. ABSx filaments are formulated to minimize these emissions, resulting in a more pleasant printing environment and reducing the need for extensive ventilation.
It is worth mentioning that ABSx Filaments by Nobufil are sustainable 3D material because it is produced from 100% recycled plastics. It significantly reduces their environmental footprint compared to traditional ABS filaments that are typically made from virgin petroleum-based sources. This sustainable approach not only addresses some of the ecological concerns associated with 3D printing materials but also aligns with growing demands for more environmentally friendly manufacturing practices.
Another important note to highlight is that ABSx isn’t the same material as ABS+. While ABS+ is produced by the Chinese brand eSun, ABSx is manufactured by the new Austrian filament brand Nobufil. Both 3D materials have different formulas developed on the standard ABS polymer.
Each material requires its own specific printing settings.
The best printing settings for ABSx filament:
Nobufil gives us the next standard 3D printer setting for ABSx Filaments:
- Print temperature: 260°C ± 10
- Bed temp: 100°C ± 10
- Printing surface: textured PEI sheet
- Fan speed: max 15%
However, these settings can be adopted and improved based on your 3D printer. For example, the Generic ABS settings in Prusa slicer and BambuLab slicer will also give good prints.
If you are 3D printing ABSx with Bambulab printers, check out our recommended 3D printing profiles for Bambulab.
To sum it up: while traditional ABS remains a popular choice for its mechanical properties and durability, ABSx filaments by Nobufil, present an innovative alternative that not only retains the advantageous attributes of ABS but also improves upon its ease of use and environmental impact. With ABSx, you get a more eco-friendly solution without sacrificing performance. This makes ABSx a particularly attractive option for both individuals and businesses looking to balance functionality with environmental responsibility in their 3D printing projects.

Alternatives to ABS 3D Filaments
The world of 3D printing is constantly developing and comes up with new 3D materials. Nowadays, we have a big choice of 3D filaments by material, color, sustainability and type of application. Let’s have a look at the 3D material alternatives when it comes to 3D printing with ABS.
ABS 3D Material Plastic Alternatives:
Are you choosing the plastic 3D filament? Then these ABS alternatives can work for you:
ABSx (by Nobufil). It is a modified ABS material made from 100% recycled plastic. We mention it here because it differs from the regular ABS by having increased toughness, chemical resistance, decreased odor in printing and, most importantly, by its ease in 3D printing. You can use it for any kind of 3D printers, even those that don’t have an enclosure. It prints as butter and as easy as PLA, offering you all common ABS advantages.
PLA (Polylactic Acid): A biodegradable thermoplastic made from renewable resources, ideal for beginners due to its ease of use.
PETG (Polyethylene Terephthalate Glycol): Offers a good balance between ease of use (like PLA) and durability (like ABS), with added benefits of being food safe and more weather resistant.
PCTG (Polyethylene Terephthalate Glycol-modified): A variant of PETG with enhanced properties such as higher impact resistance, clarity, and chemical resistance, making it an ideal choice for applications requiring durability without sacrificing aesthetics.
TPU (Thermoplastic Polyurethane): A flexible, rubber-like material that's great for printing parts requiring elasticity and shock absorption.
ASA (Acrylonitrile Styrene Acrylate): Similar to ABS in strength and durability but with better UV resistance, making it ideal for outdoor applications.
Nylon: Known for its strength, flexibility, and durability, making it suitable for functional parts that require toughness and resistance to wear and tear.
ABS 3D Material Alternatives By Type of 3D Application
Here are the ABS 3D material alternatives by its most used applications:
Prototyping: PLA is widely used for prototyping due to its ease of printing and good detail resolution.
Functional Parts: Nylon, PETG and PCTG are excellent choices for functional parts due to their durability and resistance to chemicals and temperatures.
Outdoor Use: ASA filaments’ UV resistance makes it superior for outdoor applications where weatherability is crucial.
Mechanical Parts: Nylon's strength and durability make it ideal for mechanical parts, gears, and components requiring high toughness.
High-Strength Functional Parts and Prototypes: ABS CF and PC CF are particularly suitable for creating parts that require high strength, stiffness, and temperature resistance.
Precision and Dimensional Stability: PETG CF is excellent for parts requiring precision, minimal shrinkage, and improved rigidity.
ABS Material Alternatives By High Toughness
You would like to get a durable 3D printing material, here are more options for you:
High Toughness and Durability: Nylon stands out for high-stress applications due to its excellent strength, flexibility, and wear resistance.
Moderate Toughness: PETG offers a good compromise between toughness and ease of use, being more durable than PLA but easier to print than ABS.
Flexibility and Impact Resistance: TPU provides unique properties of flexibility and shock absorption, ideal for parts that need to bend or stretch.
Weather Resistance for Tough Applications: ASA is specifically designed for outdoor use with its high toughness and superior resistance to UV light and weather conditions, making it a durable alternative to ABS for applications exposed to the elements.
Exceptional Toughness and High-Temperature Resistance: PC CF stands out for applications that demand the highest levels of toughness, temperature resistance, and durability.
Enhanced Mechanical Strength: ABS CF and ASA CF provide superior mechanical strength and stiffness, suitable for structural components and outdoor applications where durability is key.
Improved Rigidity with Minimal Warping: PETG CF offers an enhanced structural integrity, making it a great choice for functional parts requiring rigidity and thermal stability.
High-Performance Thermoplastic 3D Filament Alternatives:
The choice of the right 3D material will depend on the specific part's functional requirements, including mechanical strength, heat resistance, electrical conductivity, or the need for special properties like flexibility or impact resistance. Here are some alternatives to ABS 3D printing filaments:
PEEK (Polyether Ether Ketone): Known for its exceptional heat resistance, mechanical strength, and chemical resistance, PEEK is ideal for printing high-performance parts that must endure extreme conditions. However, its printing requirements are stringent, needing high extruder temperatures and a heated chamber.
PEI: Similar to PEEK in terms of temperature resistance and mechanical properties, PEI (Polyetherimide) is another high-performance polymer suitable for parts that require durability and high temperature resistance. It also requires high-temperature printing conditions.
PC (Polycarbonate): Beyond its carbon fiber-reinforced variant, standard polycarbonate offers excellent toughness, heat resistance, and transparency, making it suitable for printing parts like protective covers and parts that operate under stress.
PP (Polypropylene): Known for its fatigue resistance, chemical resistance, and elasticity, PP is a good choice for parts that require flexibility and durability, such as hinges or snap-fit components.
We hope you found a necessary alternative 3D Filament to ABS with these options.
FAQ: Frequently Asked Questions about ABS 3D Filaments
ABS, or Acrylonitrile Butadiene Styrene, is a thermoplastic polymer widely used in 3D printing. It's known for its high strength, gloss, and toughness, making it a preferred choice for a wide range of applications.
2. Why Use ABS Printing?
3D print with ABS for its high durability, impact resistance, and heat resistance, which makes it ideal for creating functional parts that need to withstand stress, such as automotive components or electronic housings.
3. How to Prevent Warping in ABS Prints?
Warping is a common issue with ABS material due to its contraction as it cools. Strategies to mitigate warping include using a heated bed (recommended temperature around 110°C), ensuring the printing environment is draft-free, and applying adhesives like ABS slurry or using a PEI print surface for better adhesion.
4. Is it safe to print ABS indoors?
ABS filament is known to emit fumes that can be harmful if inhaled in large quantities, making ventilation crucial. The smell and potential health risks associated with ABS printing underscore the importance of printing in a well-ventilated area or using an enclosed printer with a filter.
5. What are the best printing settings for ABS filaments?
Getting the best results from ABS 3D printer filament involves dialing in the right print settings. This includes setting your nozzle temperature between 220-260°C, bed temperature to 95-110°C, and adjusting print speed and layer height to balance detail and strength. It's also recommended to use minimal cooling for better layer adhesion.
6. How much ventilation does ABS need?
Printing with ABS requires a good ventilation due to the fumes it emits when heated. 3D printing in a well-ventilated area or using an enclosed printer with an active air filtration system is recommended to minimize exposure to potentially harmful vapors. The best move would be to have an enclosure, airflow fan, filtration unit, exhaust fan and/or window.
7. Printing with ABS vs. PLA
ABS 3D Material offers higher temperature resistance and durability compared to PLA filaments, making it suitable for functional parts. However, it is more prone to warping and requires a heated bed, unlike PLA, which is easier to print and more environmentally friendly but less durable. Unless you are using ABSx which prints as easy as PLA.
8. Why Does ABS Warp More Than PLA?
ABS material warps more due to its higher melting temperature and greater contraction rate as it cools. Managing the cooling process carefully and ensuring a stable print environment can help reduce ABS warping.
9. Should I Print with ABS or PETG?
The choice between ABS and PETG filaments depends on the specific requirements of the print. PETG offers a good balance between ease of printing and mechanical properties, with better UV stability and moisture resistance than ABS, making it suitable for a wider range of applications without the need for strict temperature controls.
10. What is ABSx Filament?
ABSx filaments (those are Nobufil ABS), are engineered versions of ABS 3D material that enhances certain aspects like better layer adhesion, reduced warping, lower odor emissions and higher print detalization. The "x" in ABSx stands for various enhancements made to the base ABS polymer to meet specific needs or overcome common printing challenges associated with standard ABS material.
11. Is ABSx and ABS plus the same?
ABSx isn’t the same material as ABS+. While ABS+ is produced by the Chinese brand eSun, ABSx is manufactured by the new Austrian filament brand Nobufil. Both 3D materials have different formulas developed on the standard ABS polymer.
12. ABS vs ABS+ vs ABSx Filaments
ABS or or Acrylonitrile Butadiene Styrene is one of the most used plastic 3D printing filaments. ABS plus and ABSx are further developments of this 3D material. ABS+ and ABSx filaments have increased toughness, better layer adhesion and are easier to print than ABS. ABSx material is also way more sustainable than ABS and ABS plus since it is made from recycled plastic and it differs by decreased odor in printing (there is almost no odor).
13. ABS vs ABS CF Filaments
ABS CF is a standard ABS material (Acrylonitrile Butadiene Styrene) reinforced with carbon fibers. The carbon fibers give the filament improved rigidity compared to a standard ABS. These carbon fibers significantly improve the material's rigidity, making ABS CF a more robust option for 3D printing applications requiring high strength and stiffness. They also improve the dimensional stability, reduce warping and shrinkage issues, and make the whole printing process easier.
14. Should I Dry ABS Filament?
Yes, drying ABS 3D printing filament before printing is recommended if it has absorbed moisture from the air, which can lead to printing issues like popping or steam bubbles in the print. Drying ABS matt filaments can make your prints even better. In any case, drying the filament in a filament dryer or an oven at a low temperature can improve print quality.
15. What is ABS Filament Best For?
ABS is best for printing durable, high-strength parts that require heat resistance and toughness, such as mechanical parts, tools, and enclosures for electronics.
16. Is ABS Filament Hard to Print?
ABS can be challenging to print due to its tendency to warp and the need for precise temperature control. However, with the right settings and environmental controls, such as a heated bed and enclosure, these challenges can be overcome. However, Nobufil ABSx with an improved ABS formula prints much easier even without enclosure.
17. Is ASA the same as ABS?
ASA and ABS are similar but not the same. ASA provides better UV resistance and less environmental impact compared to ABS, making it suitable for outdoor applications.
Conlusion
ABS filament remains a key player in the ever-evolving narrative of 3D printing. Known for its durability, heat resistance, and versatility, ABS material stands as a popular go-to material for a huge number of technical applications: from functional prototyping and DIY art projects to 3D printing prosthetics and robotic components.
This 3D plastic filament has many advantages like high toughness, heat resistance and easiness in post-processing with acetone and pains. However, its main disadvantage is, basically, that 3d printing with ABS is not as easy as using PLA or PETG and it stinks! The main ABS challenges for beginners in 3D printing is the necessity to have an enclosure for 3D printers and very good ventilation to decrease its toxic fumes.
Nonetheless, we learned that the journey of polymer fabrication marches forward, and new based-on-ABS materials like Nobufil ABSx appear in the 3D filament market. These innovative variants, engineered with a modified formula, help to overcome the traditional ABS printing challenges.
Now it becomes easier to print with ABS-like 3D materials, for example, on the usual 3d printer without any enclosure. ABSx filaments are almost odorless and also way more eco-friendly, which brings ABS back to the hobbyist and makes the 3d printing process easier and greenier for 3D printing industry experts.
We hope you found this post useful and got answers to your questions about printing with ABS Filaments.
All the best!
Comments